Unter Korrosion versteht man die Schädigung oder Verschlechterung von Materialien oder deren Eigenschaften durch Umwelteinflüsse.Die meiste Korrosion tritt in der atmosphärischen Umgebung auf, die korrosive Bestandteile und korrosive Faktoren wie Sauerstoff, Feuchtigkeit, Temperaturschwankungen und Verunreinigungen enthält.
Salzsprühkorrosion ist eine häufige und zerstörerischste Form der atmosphärischen Korrosion.Salzsprühkorrosion auf der Oberfläche von Metallmaterialien wird durch das Eindringen der in der Metalloberfläche enthaltenen Chloridionen durch die Oxidationsschicht und Schutzschicht sowie durch die interne elektrochemische Reaktion des Metalls verursacht.Gleichzeitig enthält das Chloridion eine gewisse Hydratationsenergie, die leicht in den Poren und Rissen der Metalloberfläche adsorbiert werden kann und den Sauerstoff in der Oxidschicht ersetzt, wodurch das unlösliche Oxid in lösliches Chlorid und passiviert wird Zustandsfläche in eine aktive Fläche umwandeln.
SalzKorrosionsschutzsprayDer Test ist ein Umwelttest, der hauptsächlich die künstlich simulierten Salzsprühumgebungsbedingungen nutzt, die durch Salzsprühtestgeräte erzeugt werden, um die Korrosionsbeständigkeit von Produkten oder Metallmaterialien zu bewerten.Es ist in zwei Arten von Tests unterteilt: den Expositionstest in natürlicher Umgebung und den künstlich beschleunigten Simulations-Salznebel-Umwelttest.
Bei einem künstlichen Simulationstest in einer Salzsprühumgebung wird eine Salzsprühtestkammer mit einem bestimmten Raumvolumen verwendet und mithilfe künstlicher Methoden in ihrem Raumvolumen eine Salzsprühumgebung erzeugt, um die Leistung und Qualität der Salzsprühkorrosion zu bewerten Beständigkeit von Produkten.
Die Salzkonzentration von Chlorid in der Salznebelumgebung kann ein Vielfaches oder ein Dutzend Mal so hoch sein wie der Salznebelgehalt in der normalen natürlichen Umgebung, wodurch die Korrosionsrate erheblich zunimmt und die Zeit bis zum Erhalt der Ergebnisse erheblich verkürzt wird.Beispielsweise kann es ein Jahr dauern, bis die Korrosion auftritt, wenn eine Produktprobe in einer natürlichen Umgebung getestet wird, während ähnliche Testergebnisse bereits nach 24 Stunden in einer künstlichen Simulationsumgebung mit Salzsprühnebel erzielt werden können.
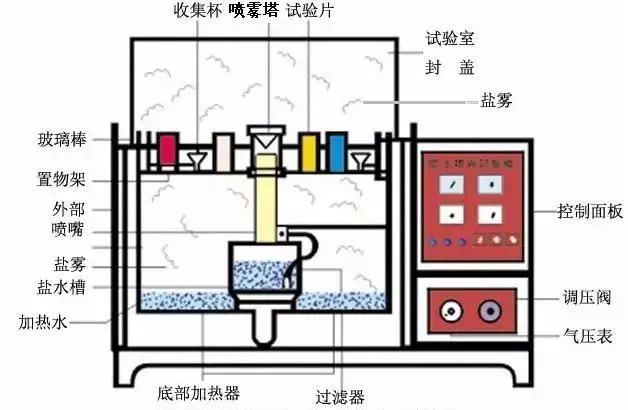
Im Labor simulierter Salznebel kann in vier Kategorien unterteilt werden.
(1) Der Neutralsalzsprühtest (NSS-Test) ist die älteste und am weitesten verbreitete beschleunigte Korrosionstestmethode.Als Sprühlösung wird eine 5 %ige Natriumchlorid-Salzwasserlösung verwendet, deren pH-Wert auf einen neutralen Bereich (6,5–7,2) eingestellt ist.Die Testtemperatur beträgt 35 °C und die erforderliche Sedimentationsrate des Salznebels beträgt 1–2 ml/80 cm/h.
(2) Der Essigsäure-Salzsprühtest (ASS-Test) wurde auf der Grundlage des neutralen Salzsprühtests entwickelt.Es liegt in einer 5%igen Natriumchloridlösung mit etwas Eisessig vor, so dass der pH-Wert der Lösung auf etwa 3 sinkt, die Lösung sauer wird und der gebildete Salznebel schließlich durch neutralen Salznebel sauer wird.Seine Korrosionsrate ist etwa dreimal schneller als beim NSS-Test.
(3) Der Kupfersalz-beschleunigte Acetatsprühtest (CASS-Test) ist ein neu entwickelter ausländischer schneller Salzsprühkorrosionstest.Die Prüftemperatur beträgt 50 ℃.Der Salzlösung wird eine kleine Menge Kupfersalz-Kupferchlorid zugesetzt, um eine starke Korrosion hervorzurufen.Seine Korrosionsrate ist etwa achtmal so hoch wie die des NSS-Tests.
(4) Der alternierende Salzsprühtest ist ein umfassender Salzsprühtest, bei dem es sich eigentlich um einen neutralen Salzsprühtest plus Test mit konstanter Luftfeuchtigkeit und Hitze handelt.Es wird hauptsächlich für Hohlraumprodukte verwendet.Durch das Eindringen der Gezeitenumgebung entsteht Salzsprühkorrosion nicht nur auf der Oberfläche, sondern auch im Inneren des Produkts.Das Produkt wird abwechselnd der Salznebel- und Feuchtigkeits- und Wärmeumgebung ausgesetzt. Anschließend sollten die elektrischen und mechanischen Eigenschaften des Produkts auf etwaige Änderungen untersucht werden.
Ergebnisermittlung
Das Prüfergebnis des Salzsprühnebeltests wird in der Regel eher in qualitativer als in quantitativer Form angegeben.Es gibt vier spezifische Bestimmungsmethoden.
(1) Rating-Bestimmungsmethode.
Bei dieser Methode wird das Verhältnis der Korrosionsfläche zur Gesamtfläche in mehrere Stufen unterteilt und eine bestimmte Stufe als qualifizierte Grundlage für die Bestimmung bestimmt.Diese Methode eignet sich zur Auswertung flacher Proben.
(2) Wiegebestimmungsmethode.
Berechnen Sie durch Wiegen des Gewichts der Probe vor und nach dem Korrosionstest den durch Korrosion verlorenen Gewichtsverlust und beurteilen Sie den WertKorrosionsschutz aufsprühenQualität der Probe.Diese Methode eignet sich besonders zur Beurteilung der Korrosionsbeständigkeit bestimmter Metalle.
(3) Methode zur statistischen Analyse von Korrosionsdaten.
Diese Methode bietet das Vertrauensniveau für die Planung von Korrosionstests, die Analyse von Korrosionsdaten und die Bestimmung von Korrosionsdaten, die hauptsächlich für die Analyse und Statistik der Korrosion und nicht speziell für die Bestimmung der Produktqualität verwendet werden.
Salzsprühtest von Edelstahl
Seit seiner Erfindung im frühen 20. Jahrhundert erfreut sich der Salzsprühtest bei Anwendern korrosionsbeständiger Materialien großer Beliebtheit, da er Vorteile bietet, darunter Zeit- und Kostenersparnis, die Möglichkeit, eine Vielzahl von Materialien zu testen und einfache und klare Ergebnisse zu liefern.
In der Praxis ist der Salzsprühtest von Edelstahl am bekanntesten, und Praktiker müssen wissen, wie viele Stunden der Salzsprühtest für dieses Material dauern kann.
Materialhändler verlängern häufig die Salzsprühtestzeit von Edelstahl durch Methoden wie Passivierung oder Erhöhung des Oberflächenpoliergrades.Der kritischste Faktor ist jedoch die Zusammensetzung des Edelstahls selbst, also der Gehalt an Chrom, Molybdän und Nickel.
Je höher der Gehalt an Chrom und Molybdän ist, desto größer ist die erforderliche Korrosionsbeständigkeit, damit Lochfraß und Spaltkorrosion auftreten können.Diese Korrosionsbeständigkeit wird durch den sogenannten Pitting Resistance Equivalent (PRE)-Wert ausgedrückt: PRE = %Cr + 3,3 x %Mo.
Während Nickel die Beständigkeit von Stahl gegenüber Lochfraß und Spaltkorrosion nicht erhöht, kann es die Korrosionsrate wirksam verlangsamen, sobald der Korrosionsprozess begonnen hat.Daher schneiden austenitische rostfreie Stähle mit Nickel tendenziell bei Salzsprühtests viel besser ab und rosten viel weniger als ferritische rostfreie Stähle mit niedrigem Nickelgehalt und ähnlichen Lochfraßbeständigkeitsäquivalenten.
Es ist zu beachten, dass das SalzKorrosionsschutzsprayBeim Testen der Leistung von Edelstahl weist dieser Test erhebliche Nachteile auf.Der Chloridgehalt des Salzsprühnebels im Salzsprühtest ist extrem hoch und liegt weit über der realen Umgebung, sodass rostfreie Stähle, die in tatsächlichen Anwendungen mit sehr niedrigem Chloridgehalt korrosionsbeständig sind, auch im Salzsprühtest korrodieren.
Der Salzsprühtest verändert das Korrosionsverhalten von Edelstahl, was weder als beschleunigter Test noch als Simulationsexperiment angesehen werden kann.Die Ergebnisse sind einseitig und stehen in keinem gleichwertigen Zusammenhang mit der tatsächlichen Leistung des letztendlich verwendeten Edelstahls.
Mit dem Salzsprühtest können Sie zwar die Korrosionsbeständigkeit verschiedener Edelstahlarten vergleichen, dieser Test dient jedoch nur der Bewertung des Materials.Bei der Auswahl eines bestimmten Edelstahlmaterials liefert der Salzsprühnebeltest allein meist keine ausreichenden Informationen, da der Zusammenhang zwischen den Testbedingungen und der tatsächlichen Anwendungsumgebung selten bekannt ist.
Darüber hinaus können verschiedene Stahlkategorien nicht miteinander verglichen werden, da die beiden im Test verwendeten Materialien unterschiedliche Korrosionsmechanismen aufweisen, sodass die Testergebnisse und die Relevanz der endgültigen tatsächlichen Nutzung der Umwelt nicht gleich sind.
Zeitpunkt der Veröffentlichung: 08.07.2022